By ESG Analyst Tanguy Montandon
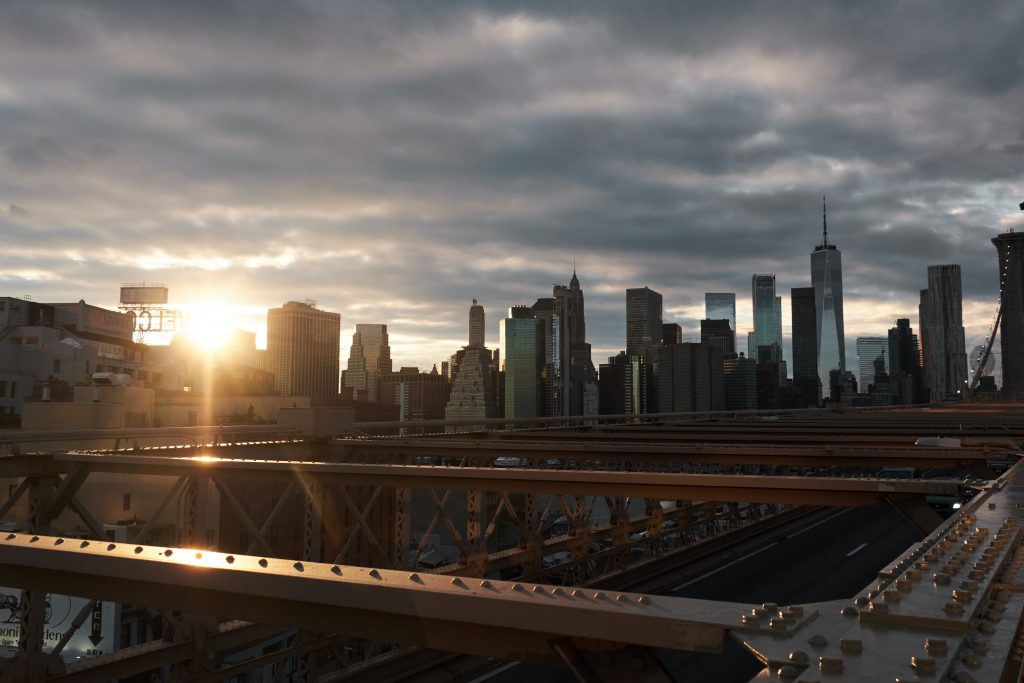
September is a fructuous month for the European industry and its transition towards net-zero emissions. Despite an economically challenging environment due to rising interest rates, Verkor was recently able to secure 2 billion euros to build a battery giga-factory in Dunkerque, France. Made possible with investments from institutional funds (such as Macquarie and Meridiam) alongside substantial public funding of 650 million euros, Verkor sets an unprecedented record. Backed up by Renault as their first client, this production facility will provide batteries to automobile manufacturers for future electric vehicles, bringing supply chains closer to consumption and limiting bottlenecks in the European market. Having achieved an impressively fast track record to remain up-to-date in a globally competitive market, the giga-factory will open in 2024 and deliver the first vehicle with a Verkor battery in 2025. By 2030, 50 gigawatt hours will be produced, the equivalent of a float of a million light EVs, such as the Renault Zoé. To put these numbers into perspective, the International Energy Agency estimates that the European demand for batteries for EVs amounted to 127.7 GWh in 2022.
Indicative of a trend likely to influence industrial and consumer goods, new infrastructure is being built in Europe to support decarbonization. As a result, European production sovereignty is increasing, challenging the Chinese almost-monopoly over battery production – 79% of the global lithium-ion battery manufacturing in 2021. EVs only represented 8.2% of the automobile market in Western Europe in 2021, but this number rose 144% compared to the year prior. With European regulations banning the sales of new combustion engine vehicles for 2035, these figures will be forced to grow and battery production must cover the entire market. Interestingly, despite labour costs which could be assumed to be too high to expect globally competitive factories in the area, these variables only account for 5 to 10% of the total production costs, with 70% allocated to materials and 20% for energy and financial amortization. With a strong emphasis on using data and AI, Verkor hopes to further optimize efficiency and remain competitive in a market where labour costs are among the highest in Europe. Furthermore, recycling expertise and technologies are growing at a remarkable pace such that, according to Verkor, a battery factory currently generates only 20% of waste. Based on their models, they hope to lower that number to 10%.
Worthy of note, Verkor is not alone in going in this direction as they are followed by ProLogium, a Taiwanese company, also planning on opening a battery factory in Dunkerque by 2026. Only 100 kilometres away at Douvrin, Stellantis, TotalEnergies, and Mercedes, also work on the first French battery factory, operational by the end of 2023. Last, but not least, Renault itself is building its own plant in 2024 in the North of France, in partnership with the Chinese group AESC-Envision. Motivated by strong policies, France hopes to see the rise of a “giga-valley of batteries”, with four giga-factories allowing the national and European market to be autonomous.
Sources:
Verkor, la pépite française de la batterie – Capital.fr
https://www.oecd.org/tax/taxing-wages-20725124.htm
Countries’ share of global lithium-ion battery production capacity | Statista
Trends in batteries – Global EV Outlook 2023 – Analysis – IEA